Editor: Trang Tran, Duc Hoang
So… What is the key to success of construction of a nearshore wind farm?
You may ask…
The answer is simple… planning…, planning … planning. You can blame it on my inherent conservative technical nature or perhaps it is true the answer is always That simple no matter how complicated the subject may sound.
What can we plan
Basically everything… you can never be over-planned… is what I would say. But the Chief Editor has put a light (virtual) tab on my shoulder to remind me that my article would have to be longer than half of a page. So I am putting down these “Lessons learnt” note in an all-reader-friendly words herewith and hope they could be useful one day for wider audience.
It comes as no surprise that preconstruction for any wind farm nearshore will need to be prepared onshore as much as possible. The key preparation comes as early as initiation stage where thorough review and approval of the construction and installation method are required. This will definitely help keeping cost stay within original budget and keeping the progress on tract
Technical Design and Piling works at planning stage
It is worth noting that the manufacture of Wind turbine components (turbines, wind towers, anchor cages, etc) and foundation components (piles, platforms, form works and pile cap rebar) are highly standardized in the market.
Standardization in the manufacturing not only saves immediate production costs for the suppliers, but also make things a lot easier downstream via ease of logistics arrangement and installation (I,e same delivery barge, same equipment for installation, etc.). More importantly, it means that much of their specifications and measurement can be made available for foundation design by the Balance of Plan EPC (BOP EPC) contractor.
One important tip here is that we could be fast-tract with the timing by engaging the BOP contractor earlier on to perform foundation and piling test via early contract whilst negotiating the Turbine Supply Agreement (TSA) with the WTG supplier.
Depending on the progress of the piling and foundation work, we should also negotiate the delivery of WTG components in “batch” to avoid putting all eggs in one basket in case we are faced with bad weather conditions, and also to enable ease of staged installation and partial COD per turbine or per group of turbines.
Nearshore Installation
The installation of WTG for a nearshore wind farm requires right types of equipment for mobilization and demobilization, taking into account different working condition factors: Water depth, wind speed, wave height, current speed, direction, tidal, etc
Whilst offshore construction commonly use Heavy Lift Vessel or Jack Up Vessel, nearshore construction uses barge or marine construction method which are generally less heavy. Although barges are lighter, they need to be sufficiently large and stable to withstand the load of 1000 tons of crane (think of 100-150 crawler crane on top of the barge!!!
This may sound contrary to general belief but swells prove to be more of a headache for nearshore wind installation than offshore. Shot but high swell can easily destabilize nearshore mobilization equipment and causes installation difficulties.
Since barges are essential for WTG installation, do expect high cost for equipment mobilization & demobilization (60% of the total BOP costs)> But sometimes, even money can’t buy the availability! Shortage of barges is not an unknown issue when all projects are racing toward the finish line of FID.
That brings us to the next tip on the “sensible planning of delivery timeline to ensure a continuous delivery and installation schedule and don’t overlook thing may seems “minor”. Like custom clearance and flexible storage availability.
Make sure you budget sufficient, buffer time for custom clearance for imported contents. Before, I forgot, it is never a bad idea to double check the supply contracts together with insurance policies to make sure that under scenarios where goods and equipment are delivered a head of schedule, someone is responsible for additional storage costs and any cost of damage during storage time.
Commissioning and partial COD
Before handing over, the turbine to the WTG commissioning team, the BOP must call for a joint-walk down with the Owner’s Engineer (OE) and WTG commissioning team to ensure safe and correct installation of all elements associated with WTGs and cables. The end result of such walk-down would hopefully be a signed off Mechanical Completion Checklist for each individual WTG to kick start commissioning activities.
According to the Electricity Authority in Vietnam EVN, partial COD test can be performed for an individual WTG (or a group of WTGs) as long as it is equipped with a dedicated metering system. A good tip is to check the local commissioning law to understand upfront what is required for partial COD in case you ever find yourself in a race against time to quantify a wind project (or partial one) under a certain revenue regime.
By now you may have realized that such useful tricks can only be planned ahead at the planning phase. Now you see why we should prepare early!
Final note at commissioning is that there will be a lot of activities (and stakeholders to manage) within relative short time window. I can readily name a few things on top of my head such as connection to the HV substation, WTG suppliers, EVN, Firefighting Department, Commissioning specialist, etc. So budget sufficient with buffer should be planned to allow errors or unexpected! As there will always be some.
I hope you do find my article entertaining and somewhat useful. Feel free to contact and subscribe for more upcoming content in the future.
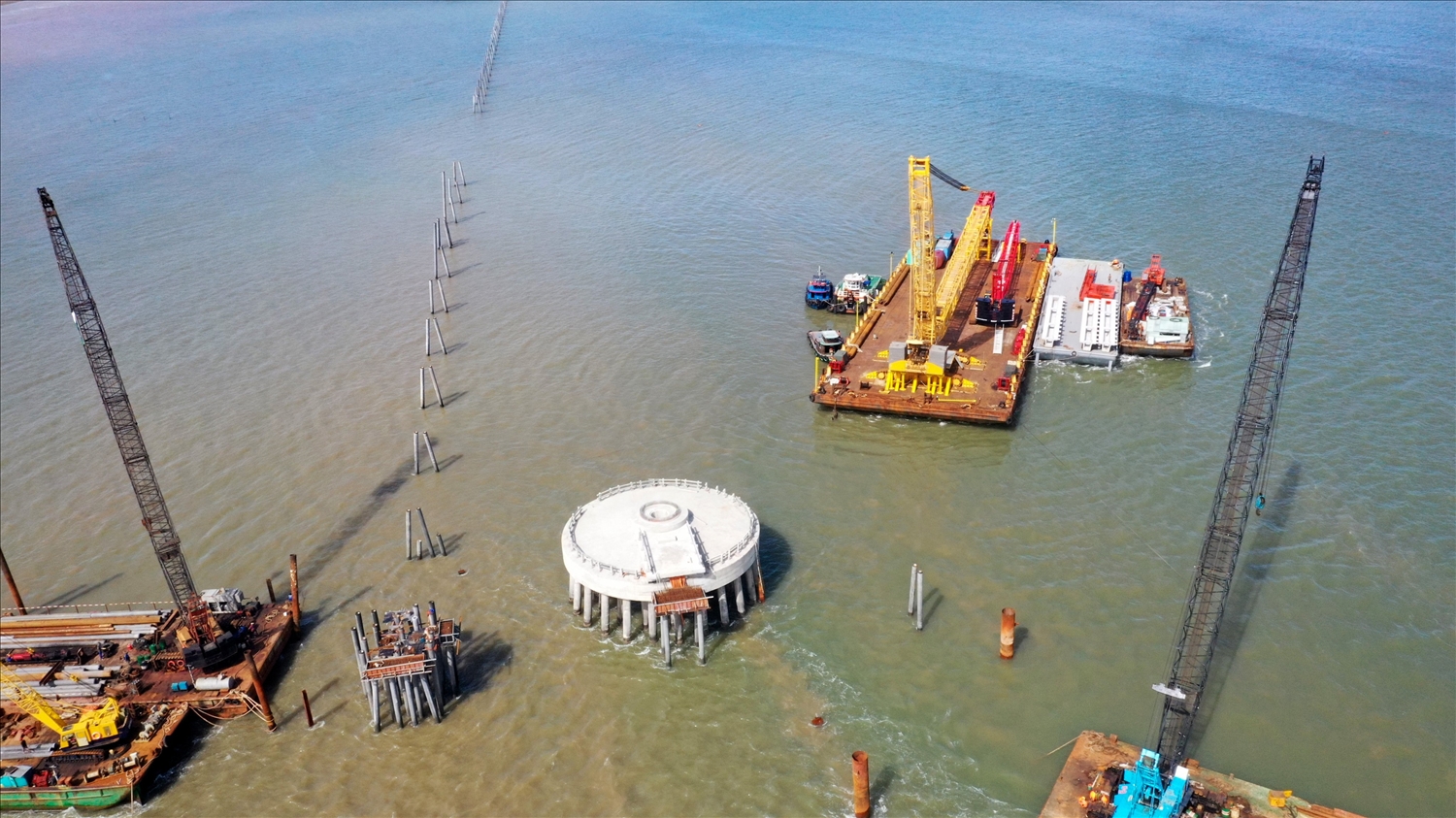